
About Meridian
​
​
Interview with Luthier Davide Cardone of Meridian Guitars by Alberto Rigoni
​
I recently discovered some incredible basses by Italian Luthier Davide Cardone of Meridian Guitars.
I was interested to learn more about his instruments so I asked him for an interview, which he accepted right away.
​
(AB) Ciao Davide, first of all thank you very much for this interview!
Could you tell us when and how you started your style in bass making?
​
(DC) Hello Alberto, thank you and a greeting to your readers. My very first experience as a Luthier goes back to about 15 years ago, when I decided it was time to try and build a bass that would enclose all the features that I appreciated in high-end musical instruments that I had played until then. The experiment didn’t turn out so well; when I first tried to string the bass, the neck cracked and the headstock fell off! But all good things need several failures before they become good things, don’t they? So, since that day I decided that, if I had to build my own instrument, I’d had to do it the way it should be done. That’s when I began studying anything that would come into my sight: manuals, articles, videos, forums, as well as instruments from other manufacturers. We have come a long way since then and I am proud to say that our instruments are having great success and that we are constantly receiving orders from all around the world.
​
​
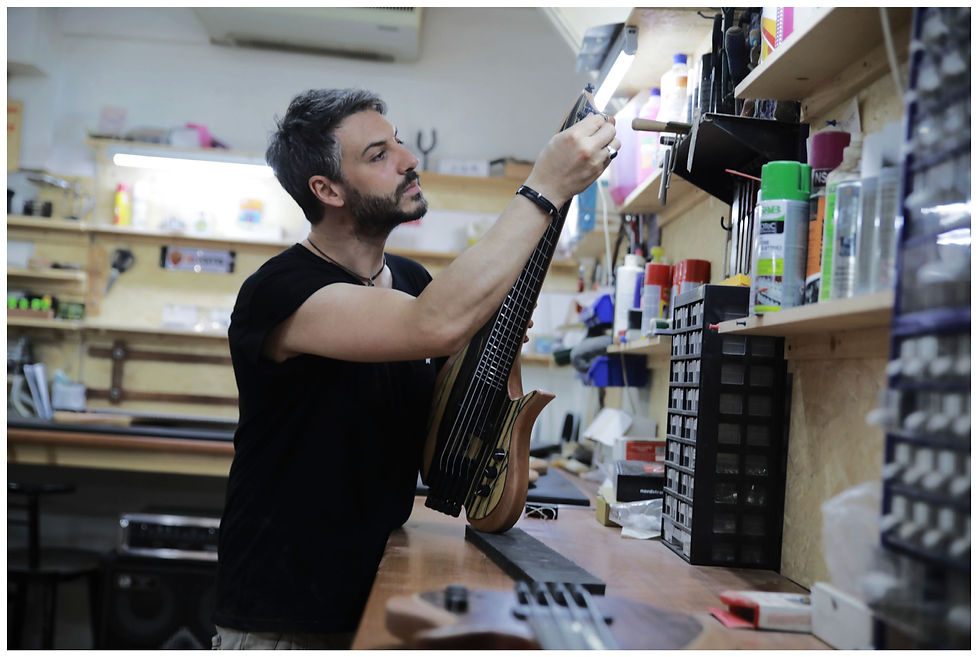
​
(AB) Could you explain your approach to the design of the instruments?
​
(DC) Designing an instrument is not an easy task at all. You have to combine many different aspects, which are all equally important, like ergonomics, aesthetics, sound and balance. So, you see, it’s really a puzzle. The designing of our Aural II required 14 months of headaches and nights on the computer to harmoniously blend the characteristics I have mentioned above. But in the end our customers always appreciate the care we take in each step of our work, and that’s what makes us happy.
Design isn't the most important thing in an instrument, but it's the thing we look at first when we want a new bass. So the design begins with an aesthetic idea, it develops and then a way is found to make the instrument work best in terms of comfort and functionality. After making the first prototypes we go back to the project to correct any details to refine the sound. As you can imagine this is a very long process, but done this way it brings great results in every aspects of ​​the instrument.
​
​
(AB) Where do you get all of your design ideas from?
​
(DC) We currently have six models in production, including a micro bass with a 22.5 inch scale called Vimana. Each one of them has very different characteristics, in order to satisfy the needs of a vast number of musicians. Yet, all our basses share the same starting module, an essential geometric shape from which we develop the instrument in its complexity: the ellipse. Starting off from a module, an archetypical form, was taught to me during my art studies.: the Gestalt Psychology is the starting point. Painting, sculpture and architecture make use of such method in exactly the same way.
I like to say that all our series are born exclusively from imagination, but it is normal that when you create something you inevitably end up taking some aspect of what you already know. In any case, Meridian basses are among the most recognisable, thanks also to the fact that they have a clearly visible stylistic unity between the various models.
​
.jpg)
​
​
(AB) What could you tell us about the tone of your instruments?
What about woods and electronics?
​
(DC) The sound is clearly one of the elements on which we work in an extremely detailed and, most of all, customized way. When a musician comes to us with his sound in mind, we spend hours talking about the details that will make a standard instrument his very own instrument. This is achieved by having the chance to choose from a wide choice of woods and pickups, as well as by installing customized electronics that will match the pickups we select. We only use world-class preamps, as John East and Mike Pope. As for the wood, we always use stocks with 25, 30 or even 35 years of seasoning, and this – I guarantee – really makes a difference. What’s more, we generally use unconventional woods, which contribute to add unique sound subtleties to every instrument.
In any case, the most important thing is to match all the essences for a good linear response, in order to have a well balanced sound without lack of frequencies.
​
(AB) What’s your opinion about the finishes used on the basses?
Do they affect the sound?
​
(DC) Finishes are one of the most important things on an instrument because they have a double impact on the final product, both aesthetic and functional. A finish must be light so that it lets the wood vibrate, as well as resistant and elastic enough to go along with the wood’s movements. It wasn’t easy to find a finish that would enclose these characteristics. Many use nitrocellulose because it allows the wood to vibrate, but then they apply 25 hands on the body to get a nice glossy look… and that literally suffocates the wood and its vibrations! I think it’s about time to get away from the sixties and from the way instruments were built back then. There are new materials now, and technologies, that are far more efficient and valid.
​
​
.jpg)
​
(AB) Is there something you would like to tell to our readers?
​
(DC) Well, first of all I’d like to thank everyone who has read this interview up to here! If you find our story interesting I’d like to encourage you to try something different from the usual three or four brands everybody knows. The world is full of talented Luthiers with brilliant ideas that build fine instruments, and I sincerely hope that, among these, you’ll come and try out one of our basses someday… because I’m pretty sure you only need to try them once to fall in love with Meridian. See you!
.jpg)